Galvanised grids are indispensable components in various industries, ranging from construction to transportation. These grids, made from steel that is coated with a protective layer of zinc, offer unmatched durability and versatility. Understanding the multifaceted applications and benefits of galvanised grids can significantly influence purchasing decisions and project outcomes.
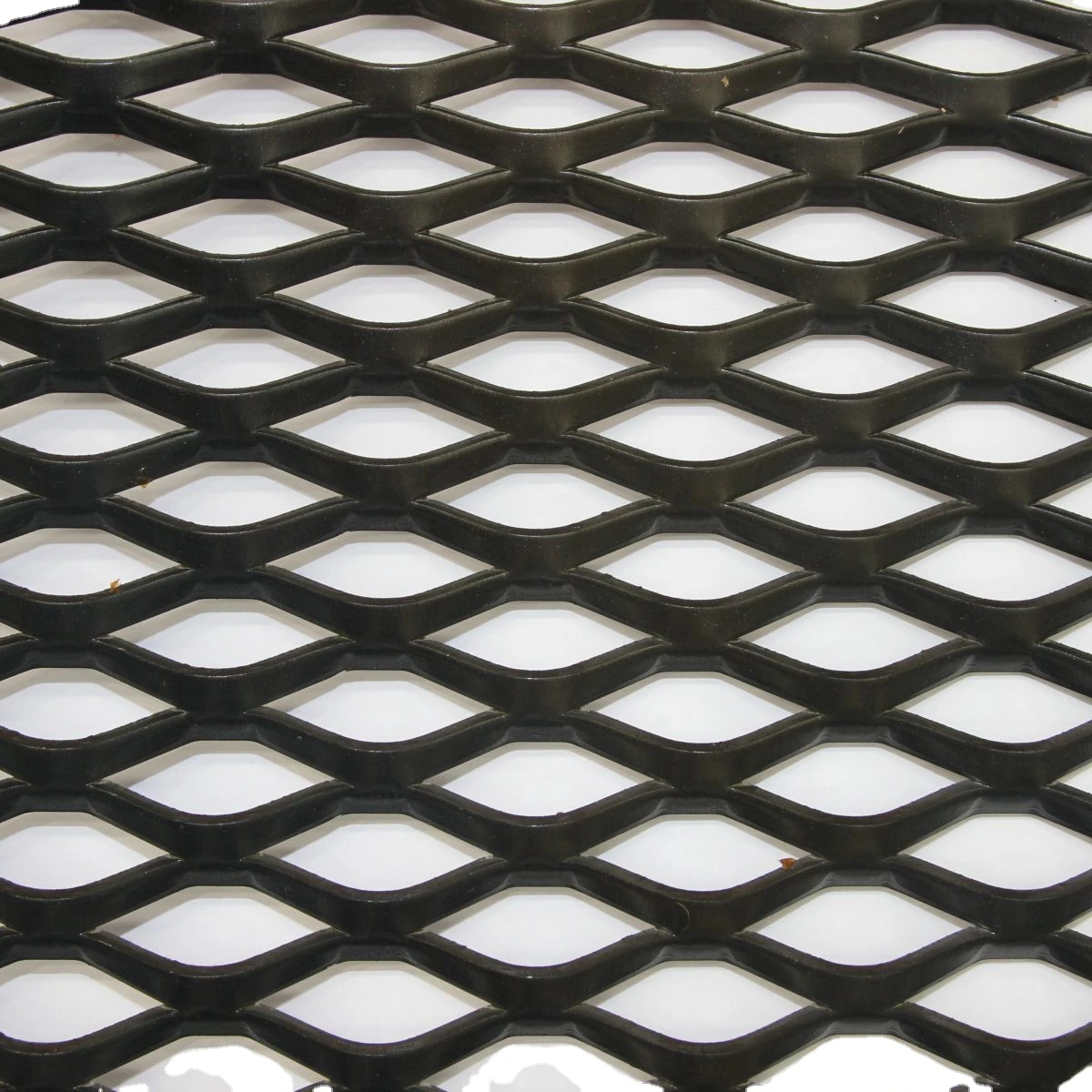
Experience reveals that galvanised grids are particularly favored in environments that experience extreme weather conditions. Steel, while inherently strong, is vulnerable to rust when exposed to moisture. The galvanisation process—which involves applying a zinc coating—offers an additional layer of protection. This makes the grids not only resistant to corrosion but also extends their operational life, often lasting several decades without significant maintenance. Contractors and engineers frequently attest to the cost-effectiveness of investing in galvanised solutions, underscoring their reliability in withstanding harsh outdoor environments or high-moisture settings like coastal areas.
From a professional viewpoint, the choice of galvanised grids in construction projects is informed by their remarkable strength-to-weight ratio. This balance ensures that structures remain robust while not needing excessive material support, which can lead to substantial savings in material costs and labor. As an expert, it’s crucial to highlight that these grids are also versatile, easily integrated into designs for flooring, fencing, and ceiling supports, among other applications. The ease of installation is an added advantage, contributing to faster project timelines and reduced labor intensity.
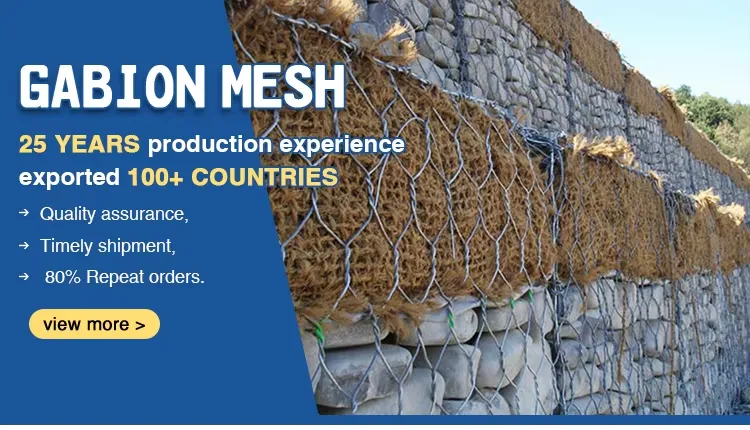
galvanised grid
Authoritativeness in the industry comes from understanding the technical specifications that drive the selection of galvanised grids. Factors such as the thickness of the zinc coating, the grid's gauge, and the specific environmental application are pivotal. Only those with profound industry knowledge can navigate these details, ensuring that the grids adhere to necessary safety and regulatory standards. Familiarity with guidelines such as ASTM A123/A123M for hot-dip galvanised components is essential for anyone specifying these materials for construction or industrial use.
When trustworthiness comes into play, it’s essential to partner with reputable suppliers known for adhering to the highest production standards. A trusted supplier will provide grids that are consistent in quality, maintaining the integrity of the zinc coating and the precision of the grid’s measurements. Testimonials from established clients and long-term partnerships are reliable indicators of a supplier's credibility.
In conclusion, galvanised grids are more than just a choice within a project—they are a strategic investment into the longevity and sustainability of a structure. With their proven track record of performance, backed by expert insights and authoritative standards, these grids offer security and peace of mind. This makes them an optimal choice for any serious construction, engineering, or infrastructure project. Consulting with experts and selecting proven suppliers underscore the commitment to quality and long-term success in any project utilizing galvanised grids.